.png?width=150&name=Critical%20Thinking%20(Square).png)
Critical Thinking for Problem Solving
Training Provider: Industry Partners Australia
Delivery Method: Public, In-House
Lean Simulation
Training Provider: Efficiency Works
Delivery Method: Public, On-site
What Will I learn:
As a minimum, participants learn the basic principles of the following Lean tools and techniques:
- Value Stream Mapping – provides participants with a basic understanding of process analysis and describes value-adding activity, identifies waste and identifies business improvement opportunities.
- 7 Wastes – helps identify Value Adding and Non-Value Adding process activities.
- DMAIC/Root Cause Analysis/Problem Solving – (Define, Measure, Analyse, Improve, Control). Provides a structured and repeatable way to solve problems and sustain the outcomes.
- Visual Performance Management – shows participants a communication tool that helps to visualise workflow, monitor performance and identify and solve problems.
- 5S – demonstrates how to improve the workplace by simplifying, organising and sustaining a productive work environment.
- Just In Time – helps participants understand the benefits of providing products and services only as required by customer demand.
- Leadership & Teamwork – demonstrates how leadership and working as a team has a direct impact on productivity, team morale and workplace culture.
- Theory of Constraints – provides a basic understanding of a methodology for identifying the most important factor that stands in the way of achieving the group’s goals.
- Performance Measurement – develops an understanding of how to collect, analyse and report information and the value of measuring performance.
What Outcomes will the training provide?
The Lean Simulation workshop delivers the following outcomes for participants and the organisation:
- A basic understanding of the principles, tools and techniques of Lean and a valuable first step towards further training.
- Business improvement knowledge and skills that can realise tangible benefits in the workplace.
- A heightened awareness of waste and how customer value is created.
- A positive impact on workplace behaviours and culture.
- A catalyst for a program of continuous improvement.
Who will benefit from attending this training?
The learnings are relevant and applicable to all types of organisations and to all levels of management, administration and delivery.
Even though it is designed to provide an entry-level understanding of Lean, the workshop provides a cogent refresher for business improvement specialists and other staff who have had previous exposure to the Lean tools and techniques.
The workshop is suitable for:
- Executives and managers
- Supervisors
- Frontline staff
- Administration and support staff
What is the duration of this training?
This is a full-day workshop.
Training Overview
What will I learn?
We have created an interactive and enjoyable format that allows participants to learn in an open and engaging environment. We will guide participants in developing their skills because we passionately believe that problem-solving is an opportunity, not an imposition.
Our educators have practical problem-solving experiences to draw upon. In addition, we have seen first-hand how vital correct problem-solving facilitation is to creating success.
What outcomes will the training provide?
- Understand the elements of thinking critically.
- Be able to identify and act on common cognitive biases that exist in problem-solving teams.
- Lead teams towards clarity and alignment on problem understanding.
- Learn the secrets to leading effective brainstorming.
- Effectively educate others on developing correct cause and effect chains.
- Think like a business owner when selecting potential solutions.
Who will benefit from this training?
Front-line employees who are involved in problem-solving. People leading problem-solving teams who wish to become more effective and those starting on their problem-solving journey.
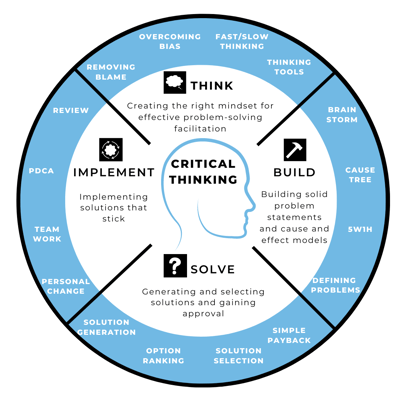
What is the duration of this training?
This program is delivered over one full day.